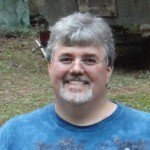
Who am I? Well these are the basics:
Don Bailey
42 year old software developer, married with boy/girl twin 7 year olds.
Hobbies: If you can hook it to a computer, I have some interest in it.
I’ll eventually get around to filling this out with some more detailed information… (yeah right).
As a fellow CNC enthusiast I encourage you to check out Freeside Atlanta (http://wiki.freesideatlanta.org/) when you get a chance. It is a local hackerspace that will hopefully be doing some cool stuff in the coming months
Sincerely,
John
Looks neat, might not fit in with my current life, but I will see if I can attend the next open meeting and check it out.
– Don B.
You do fantastic work.
I have a couple of problems getting my machine up and working. It seems that you are good at all of this. I am good at building the machine, but setting up the controller to run the motors with the software has me baffled. I have a controller and three stepper motors all hooked up, but can’t find any software (free software) to even test the motors. Ever one that gets a machine up and running makes a video of it cutting out new parts, but they never show us how they did the setup or config of the software. I am a disabled Vet. and I have been trying to get this hobby up and running for years. I don’t type or spell good, but would like to talk with you on the phone if you would. I learn better hands on and talking.
Thank you for posting your adventure, it is very informative. I’m curious on why you’re going away from the Rockcliff Model D. I have the plans and might build one. Last year I build a foamcutter of my own design and ideas used from others using drawer slides and MDF, so I got my feet wet on what it takes. Have you found a good low cost source for multi stop ACME screws? I’m using single stops from Enco and they work good provided they are cleaned/treated on a regular basis to get ride of the surface rust.
My Rockcliff model ‘D’ has been awesome, I built it with limited tools and a tight budget and it has performed beyond my expectations. I think the plans are very straight forward, and the end result works very well, anyone can build the Model ‘D’ with a few modest tools and be very happy.
The only reason I am moving away from it is that I had this desire to build the type of machine ‘kit’ that I would have liked to have been able to buy when I was just starting with the CNC machines. The idea was for a bolt together machine with a limited part count that could be shipped for a reasonable amount, that would be completed with parts purchased locally by the builder. The current version is a little more complicated than I intended, but I think it meets the goal and also has the benefit of being easily resized to met different needs. I really want to cut a few kits for sale just to see what my price point would need to be to justify the effort, not sure if I will ever do more than that.
I am debating building a foam cutter, I don’t really have a need at the moment, but it looks like a fun project. However I think my next project is going to be a vacuum forming machine, something like the Phlatformer , but maybe I bit bigger.
I have not gone to multi-start screws yet, it is in the plan but the budget keeps saying no. Enco does carry multi-start screws, but given the condition of the last order of single starts I got (had to wet sand them quite a bit to get them smooth), I am a little weary… however since they cost so much more, I would hope the quality is significantly better. The whole multi-start option is just expensive, screws, nut, couplers… I spent ~$20 on my current machine for drive components (mostly where made be me), it will be well over $200 for a ‘cheap’ 2 or 5 start set up. I have seen a number of recommendations for Roton, so I may go down that route if I get the funds… although I am not sure they are compatible with Dumpstercnc parts, so maybe not.
On a side note, I have been using a spray on Teflon lubricant and have not noticed any issues with rusting… the machines are in the garage in north Georgia so it does get humid.
Do you have any information on your creations, I would be interested in seeing the foam cutter and the results, oh and what software are you using to design/generate g-code with?
Thanks,
GrumpyGeek
How did set up emc2 to work with the gantry drives on your model D? I have built the same model and I am trying to set up EMC2 to slave on of the motors but I cannot seem to find the solution.
I pulled this bit from a post on the Rockcliff fourm: http://www.rockcliffmachine.com/forum/showthread.php?t=179
If you are running 4 motors you can slave the extra motor by setting the pins for the A axis to use the same one the primary axis uses. Keep in mind that if you do this, the slaved motor will not turn from within the stepconfig tool, but will work fine from within emc2. So you will need to set up your motors using just 3 motors, and the slaved motor will use the settings from the primary axis. Just make sure you test this before you hook to your lead screws Also make sure you set up for XYZ axises, not XYZA (then you won’t see the A axis settings).
I just wanted to update this thread with the fact that I have finally gotten around to testing the ability to slave an axis in EMC2 and it does indeed work.
…
I used the standard Xylotex settings and set the 4th Axis pins to use Y direction and step signals and it works like a dream, just remember that only the 1st motor will spin in the StepConf program, so don’t run that dual screw axis on machine from within StepConf. Hopefully they will update StepConf to handle this as well in the future, would make fine tuning the machine a bit easier.
Let me know if you need more information and I will take some screen shots and post them for you.
Grumpygeek,
VERY nice work .. I notice you have not done any updates in some time.. I hope things are still going well !!
I purchased the rockcliff plans my self last winter, I have been picking up parts online (ebay & other places) .. I have started cutting some of my MDF, and I was not happy with the long MDF on the X (with the rod) .. So I have started looking into the gas pipe type design like you have done. Your site has already given me some great ideas !
Hi Dave,
Glad you find the site interesting. I am still working on the design, I completed assembly of the latest router, made a few minor changes and have just finished cutting a set of parts for a friend. If the assembly goes well, I think I am ready to call this design done (for now), and maybe start cutting out a few kits as time allows. I am long over due for an update to the site, just haven’t made the time.
Is there a particular problem you are having with the long axis? I had to shim my bearings a bit to get them nice and tight after I glued the rod carriers in place, but they worked really well once I got everything assembled. The more time I spend designing my own router, the more I appreciate the simplicity of the Model D’s design.
Thanks,
GrumpyGeek
Grump,
I started cutting all my MDF, and I really didnt like the long X axis design with the small rod down the middle.. Thats when I was thinking about using gas pipe, I found the nice pre cut ones @ home depot. I was then back on the rockcliff forums, and stumbled on a couple of your postings..
The thought I had was a little different then your design. I was thinking about keeping my lead screw mount & bearings in the middle of the 2 pipes. and putting ajusters in to force the bearings into the pipes…
Looking forward to seeing more of your updates. I do have to agree, this could be sold in a kit form. It would need to be more “refined” and bolt together .. The only down side.. Shipping , the MDF is heavy (but its affordable) the other option would be HPDE plastic .. It would be lighter, but more money for the HPDE plastic.
Dave
Hi, very nice site!! One question: have you measured the amount of runout (T.I.R) of the Dewalt 660? It’s the only accesible (low price) one available in my country (others cost2 – 3 times of what they cost in the USA!!), but I’m concerned about the spindle having too much runout.
Thanks and have a nice day.
Alfredo.
Very nice job. I’m about to built a CNC around the same size and my first thought was to make it with extruded aluminium. But looking at some realizations on the web and specialy yours, I think I’m going to do it with MDF. I already did some jobs with this material. Your CNC inspire me a lot. I already received screw balls and shafts and I have to go slowly as I’m living in Tahiti (French Polynesia) and I have to import everything, it takes a lot of time and money.
Congratulations! And I like the colour…
Jean Jacques