For the most part is has been too cold to work on the machine for the last month or so, so I have not made a lot of progress, and I managed to crack part of the Z axis while testing the machine.
First the good stuff:
I decided to mount the power supply and electronics in a cheap storage container, which is exactly what I did with my last machine. I used an x-acto knife instead of a drill this time, and did not any issues with the plastic cracking like I did last time. However using the x-acto knife to drill this many holes by hand did lead to a couple of good sized blisters, there is a better way I am sure. This part is pretty much done with the exception of a toggle switch on the power supply AC so I can turn it off without unplugging it.
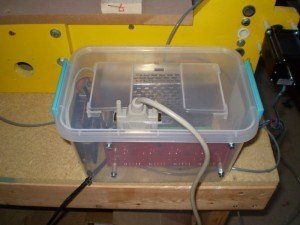
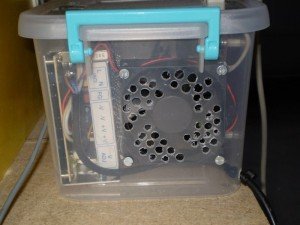
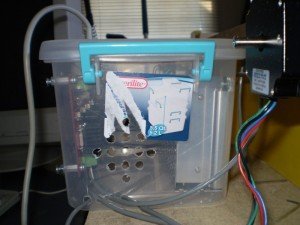
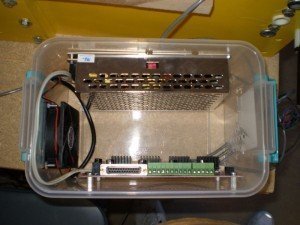
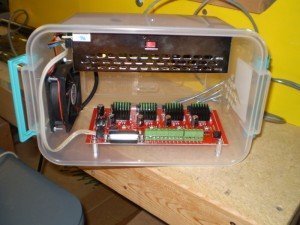
Now for the bad stuff:
After hooking up the electronics I went back to my EMC2 settings and starting adjusting them to get the maximum speed out of each axis. On the Z axis (~8″ of travel) and X axis (~24″ of travel) I was able to get about 42 IPM reliably, I backed the Z down to 12 IPM and dropped the X down to 36 IPM for good measure (As far as I can tell at the moment, EMC2 adjusts in .1 IPS, so I have to adjust in 6 inch increments). On the Y axis (~48″ of travel) I could get 36 IPM reliably, but had some issues when I got within 4″ if the motors (I need to figure out why, I am sure it is some sort of alignment problem), I backed Y down to 30 IPM. BTW adjusting the Y was somewhat of a pain since every time the one of the motors seized, I had to realign both sides. I did not have this issue with the first machine which also used dual screws, but my max speed was only 24IPM due motors and lead nuts, so I guess I never got fast enough see the issue.
I was really hoping to get speeds closer to 60IPM, some reasons I am not seeing this could be that my DIY lead nuts are too tight, there are alignment issues, or I just had unrealistic expectations, time will tell I guess.
I went ahead and ran the EMC2 default program a few times to see how things went, and had no issues. Then I got stupid and decided to tape a sharpie to piece of wood and use some C clamps to attached it to the z-axis. The first run went ok, but the pen was not secure, so the drawing was not that good. So I added some more duct tape to hold the pen more securely, re-homed EMC2 and ran again… the drawing looked better, but then I noticed that bottom of the Z axis was cracked, it seems when I reattached the pen on a stick, I put once of the clamps a little lower and it ran into the bottom pipe clamp and cracked it. I decided that rather than smash the machine, I would just go to bed. (The drawing are also backwards, but this just means I need to reverse the X axis direction…I think)
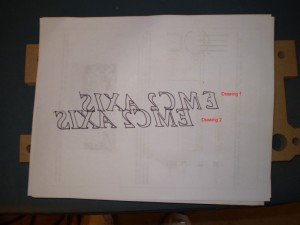
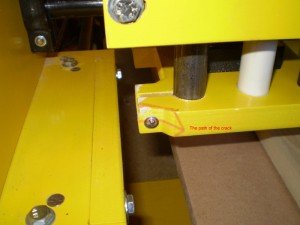
The next morning, since I now had to re-cut the part anyway, I resigned the way the pipe is attached to eliminate the splitting I had with the pipe clamping portion of the part. I cut 2 copies of the part for the top and bottom of the Z axis, and I am now waiting for a little warmer weather to paint them and attached to the machine… hopefully soon.
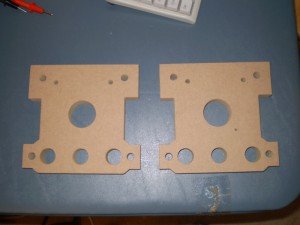